Transportation Market
Explore the basics of this market plus articles, videos, webinars, selection guides, white papers, manufacturers and more…
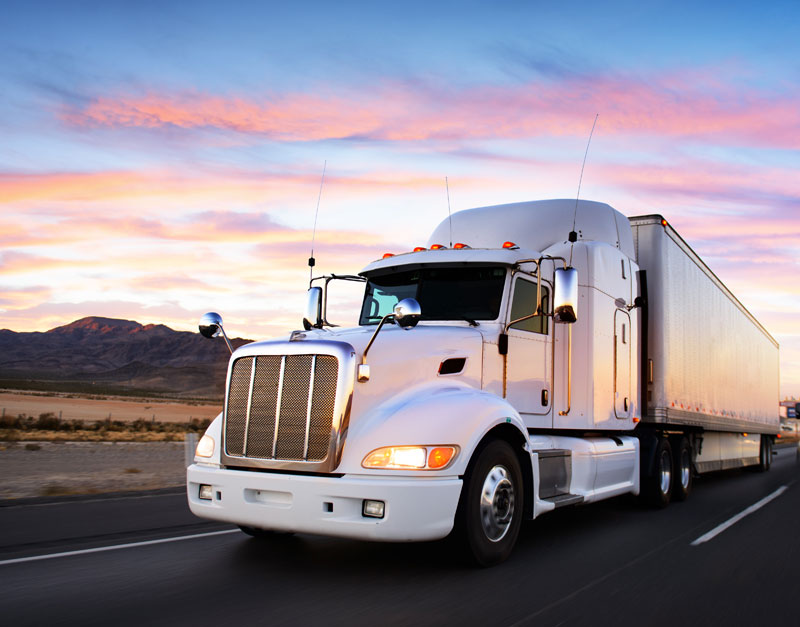
How adhesives are used in the transportation market...
The transportation market uses adhesives and sealants widely for the manufacture of cars, trucks, buses, aerospace (planes, rockets, space vehicles), boats, trains, etc. They are widely used to decrease weight (adhesive bonding vs. mechanical), increase durability, energy efficiency, safety, sustainability, and to comply with stringent regulations.
Structural adhesive applications include joint sealing, magnet bonding, metal bonding, multiple surface bonding, noise, vibration, and harshness (NVH), plastic and composite bonding, potting and encapsulating, and more.
The Transportation & Marine Market is quite extensive and includes thousands of applications in such areas as:
- Aircraft & Aerospace
- Automotive Module Sealing using
- Liquid Gasket Sealants
- Electronic Circuit Board Protection using Liquid Potting and Encapsulants
- Exterior Vehicle Trim
- Interior Vehicle Trim
- Marine
- Powertrain and Under-the-Hood Components
- Rail
- Vehicle Assembly
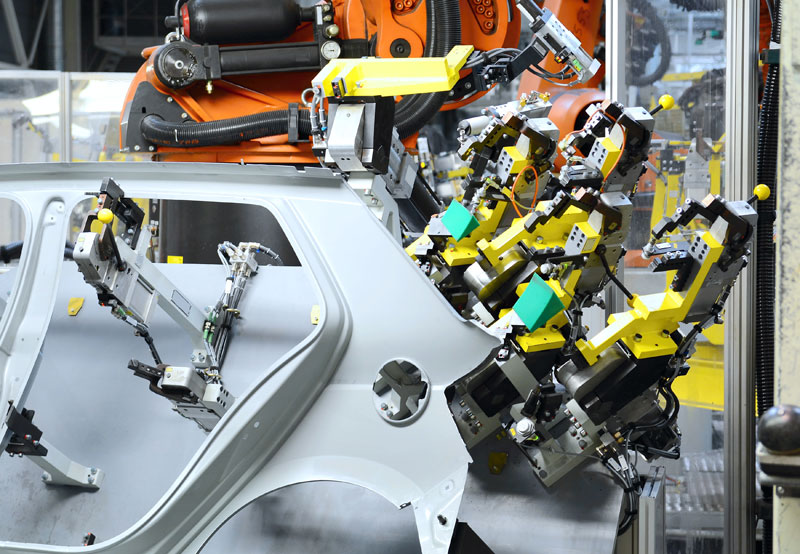
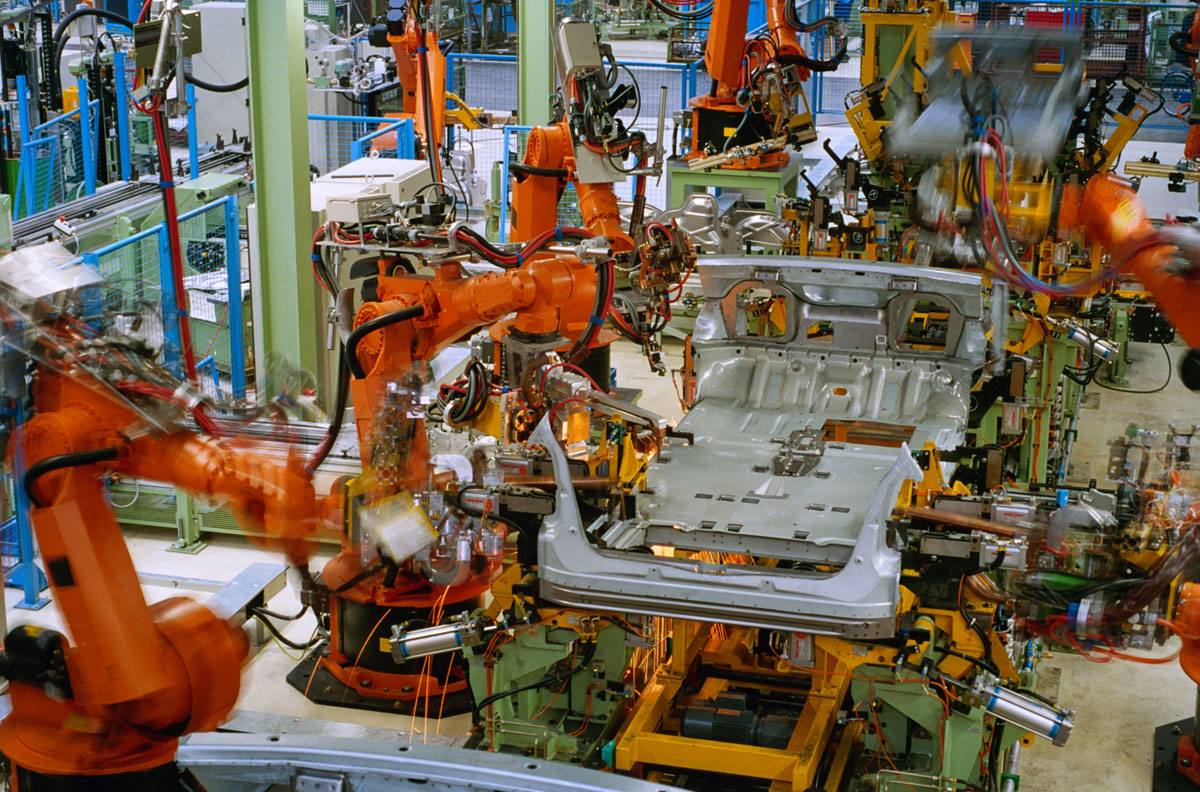
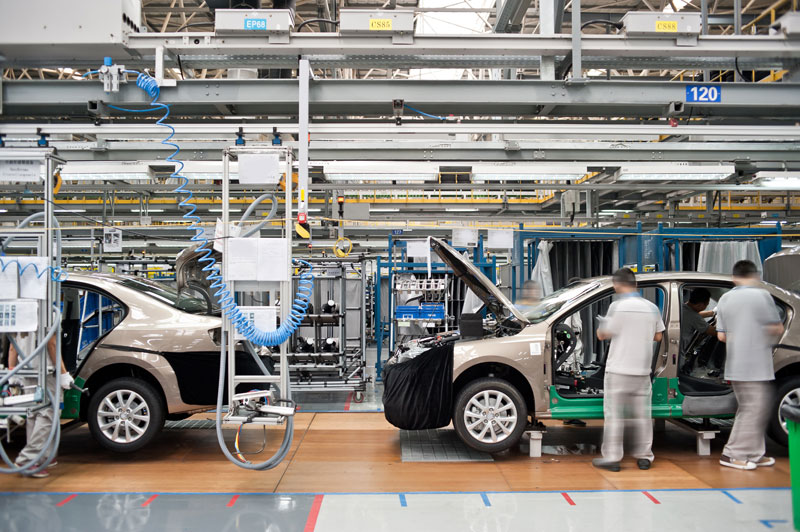
Bonding Metal Sheets in Vehicle Bodywork Construction
Car bodies largely comprise steel sheets having a thickness of 0.6 to 0.8 mm. The trend in modern car bodies is towards a flatter design with as little wind resistance as possible, low weight and hence ultimately reduced fuel consumption. Flat components such as the hood and trunk, and also door and roof panels, are affixed to ridge-like struts and are hence stiffened. The most common method for joining bodywork components, namely spot welding, cannot be used on the flat visible sides because this would result in unsightly points and these would require time-consuming work (filling) to repair. The use of adhesives to solve this problem was introduced about 40 years ago – adhesives are used to join the components together and the number of welding points was reduced to a small number at the edges. The bonding process had to be introduced into the relevant production line sequence.
The construction of car bodies puts extremely high demands on structural bonding technology: Special surface pretreatment of the metal sheets, which is essential for creating high-strength bonds having high stability, is not possible on a mass production line. In addition, the substrates are also still coated with corrosion protection oils during the production process. These can only be removed before the final process step.
Key requirements of adhesives for use in vehicle bodywork construction include:
- Ability to form structural bonds with defined properties over the lifetime of the component under operating loads;
- Stability at 170 to 230°C for ca. 30 minutes during the painting/lacquering process;
- Resistance to running and washing away in the non-cured state;
- Ability to be processed automatically;
- Ability to penetrate for spot-welds as crack stoppers.
Only hot curing adhesives meet the above mentioned requirements. The adhesives specially developed for these applications (curing at 180 to 230°C) are formulated in such a way that in the non-cured state up to 20 weight percent of oil can be taken up via dissolution. However, in practice when using the adhesive, so much oil is forced away by the adhesive that immediate initial bonding of the adhesive is usually guaranteed. The remaining oil is taken up by the adhesive and forms part of the adhesive film.
The high temperatures accelerate the dissolution of the oil by the adhesive. The oil is essentially uniformly distributed in the cured adhesive film and does not diffuse back to the surface.
Crash tests make clear that the alternating fatigue strength and the energy absorption, even after aging, can be considerably improved by using adhesives for some of the joints, compared to wholly spot-welded constructions. The current state-of-the-art involves a combination of bonding and spot welding, so-called spot-weld bonding, and this is used on a large scale for vehicle bodywork construction.
The following adhesives are used for bonding sheet metal in vehicle bodywork construction: Plastisol adhesives, essentially filler-containing pastes comprising powder-form PVC, plasticisers and adhesion promoters. For special applications, single component hot curing epoxy resin adhesives are used.
Example applications are: stiffening and flange seams on hoods and trunks, doors and roof structures.
Looking for more information on adhesives & sealants use in vehicles? Visit the cars, trucks & buses sub-market page to explore more.
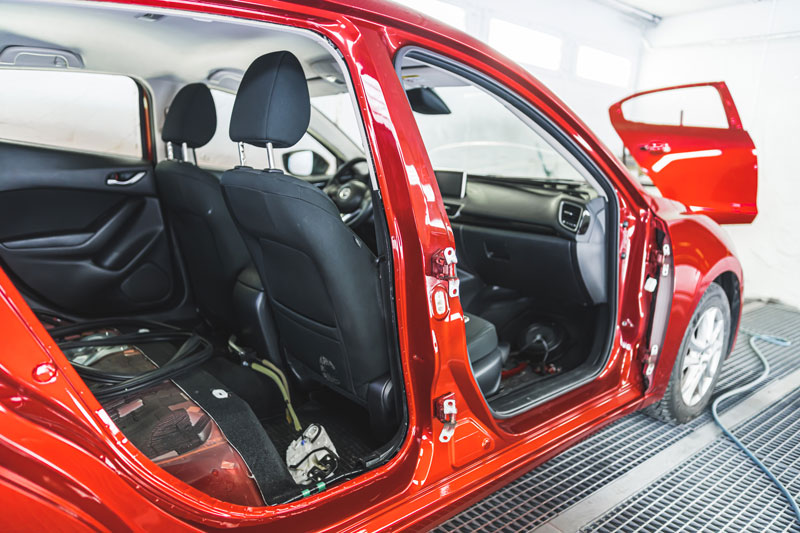
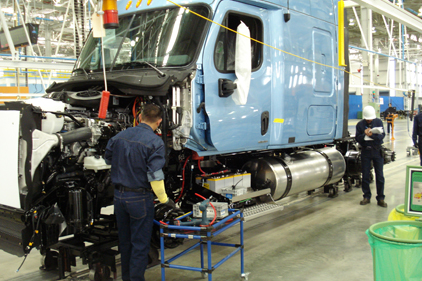
Safer Cars With Adhesives
“Glued cars” are safer and more economical. It is no wonder then that adhesives have entered what used to be the domain of welding in the automotive industry. For instance, in 2001, 33 linear feet (about 10 meters) of adhesive were used for the body of the BMW 7 model, today 500 linear feet (about 150 meters) are used. About 9% of annual adhesive production is used in vehicle construction.
Today a car contains up to 40 lb (18 kg) of adhesives. And for good reason: crash tests have demonstrated that glued cars do better than welded designs. What is more, adhesives do not affect how parts are assembled. Other techniques including welding, riveting or bolting impact the rigidity of assembly materials. In the event of an accident, adhesives behave like a buffer. That said, automotive engineers design car bodies so that as much impact energy as possible is transformed into deformation energy, rendering it harmless. This gives maximum protection to passengers. Today, so called crash-resistant adhesives are used for this purpose. However enhanced safety is not the only benefit of adhesives in vehicle production. If doors were welded, the outside would have to be laboriously reworked to ensure a good appearance.
For glued doors though, there is no need for reworking, resulting in lower production costs. In order to ensure that the windshield, which is subject to enormous loads (imagine the headwind when riding down the highway at 80 mph) and remains perfectly in place in the frame, the automotive industry uses advanced high performance adhesives. These guarantee perfect hold overall, even under extreme conditions including wind, rain or hailstorm,blistering heat in the summer or bitter frost in the winter. Directly glued front and rear screens ensure lower air resistance, thereby reducing gas consumption.
For modern cars, manufacturers use a range of materials besides steel sheets. This mix of materials is also held together by adhesive. Incidentally, the use of adhesives is not limited to car production but is used in other vehicles as well. While an average rail car built between 1981 and 1993 contained some 22 lb (10 kg) of adhesive, some modern rail cars used today weigh in with up to 1100 lb (500 kg) of adhesive.
Looking for more information on adhesives & sealants use in vehicles? Visit the cars, trucks & buses sub-market page to explore more.
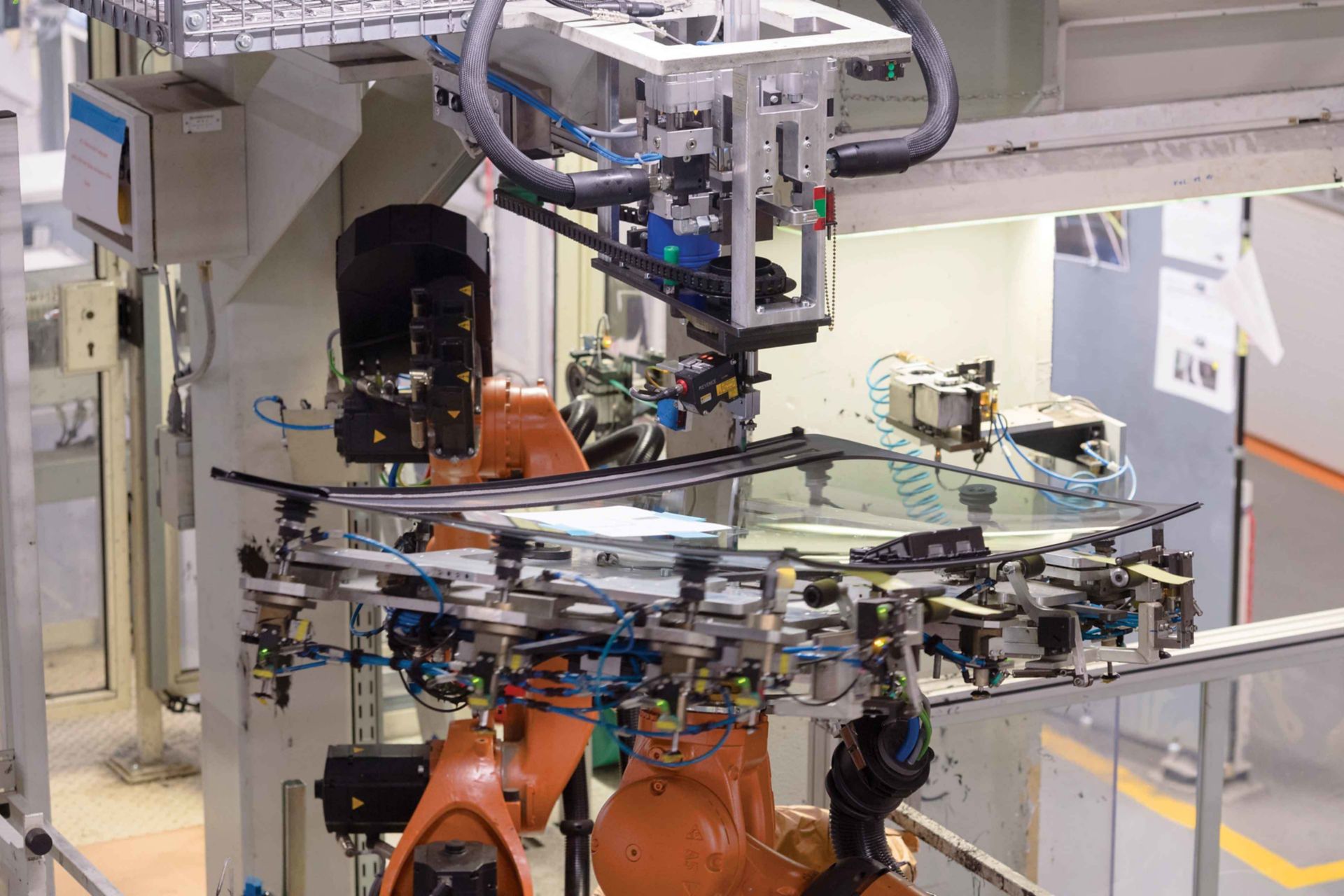
Direct Glazing – Glass Bonding Into Automobile Bodywork
The panes of glass are fitted after painting and lacquering the car bodywork. In days gone by, the front and rear windscreens were fitted into the bodywork using a profile made of an elastomer that surrounded the glass. A cord-like tacky elastomer sealant was then applied to improve the seal.
Since the start of the 1970s, so-called direct glazing has been increasingly used. Moisture curing 1-component (1-C) polyurethane adhesives, or alternatively modified siloxanes (MS) polymers are used for this. Besides providing an excellent seal, the advantages of this technology are that larger panes of glass can be used and this reduces the overall weight of the car bodywork. This is because the glass panes become a structural material due to the adhesive curing as an elastomer. The rigidity of the structure therefore increases and this so allows thinner metal sheets to be employed.
Looking for more information on adhesives & sealants use in vehicles? Visit the cars, trucks & buses sub-market page to explore more.
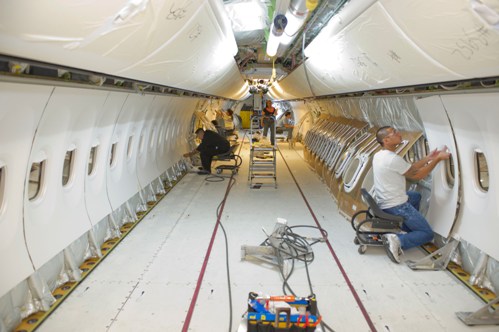
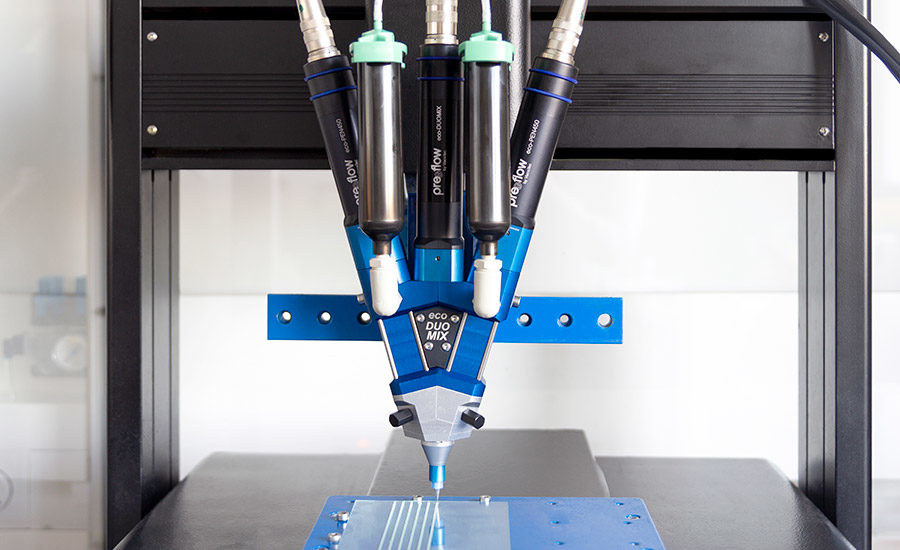
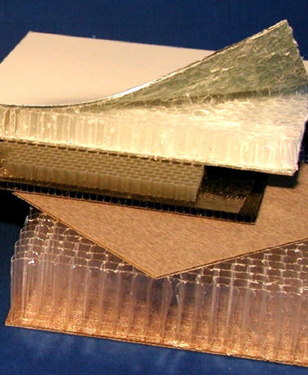
Aircraft Manufacturing
The development of flight over the last six decades is pretty impressive. Today we jet all over the earth as if it were the most natural thing in the world. However, no less impressive is the development of adhesives during the same period. Over the years, this practical household helper has become a high-tech tool.
For several decades now, bonding has been one of the most important joining techniques in aircraft manufacture. The specific reasons for this include the fact that bonds have lifetimes of up to 30 years, high resistance to dynamic loads and media and resistance to extreme, and sometimes very rapid, temperature changes, from sub-zero temperatures in the stratosphere to ground-level temperatures in desert climates.
For several decades now, bonding has been one of the most important joining techniques in aircraft manufacture. The specific reasons for this include the fact that bonds have lifetimes of up to 30 years, high resistance to dynamic loads and media and resistance to extreme, and sometimes very rapid, temperature changes, from sub-zero temperatures in the stratosphere to ground-level temperatures in desert climates.
One advantage of the adhesive elements in paste form is obvious. Because of its consistency, it can also be used locally and its compensatory tolerances allow for a stable bond. Also, it offers high stability because the use of adhesives allows the structure to remain intact during the binding process. This offers the chance for new composite materials to be developed.
Weight reduction is an economically advantageous aspect, in addition to the technical advantages offered by adhesives. Every pound that is saved reduces the operating costs of an aircraft; and savings in the production costs and — based on the overall life of the vehicle extremely important for the auto and aviation industry. The application of bonding technology in aircraft manufacture allows extremely lightweight design due to the consequent use of light metal alloys, fibre-reinforced plastics and so-called sandwich components. Bonding is used for internal structures for manufacturing structures with lightweight honeycomb sheets.
It is also used for creating high stress joints, so-called primary structures, for example for the external stiffening of sheet metal of differing geometric size, for sandwich structures made of aluminium or plastic honeycombs with bonded on veneers and for bonding stacks of sheets. The Airbus vertical tail is an example of this. It is composed of an aluminium lattice framework and veneers made of carbon-fibre reinforced epoxy resin adhesive. The individual components of the veneers are pre-cured and the whole component is bonded in an autoclave.
In the aircraft manufacturing industry, it is mainly epoxy resin adhesives, especially prefabricated films with a curing temperature of at least 120°C, that are used for bonding sheet and sandwich components. The lap shear strengths that can be attained are about 20 MPa (static) and 1 MPa (dynamic). The effect of peel forces is avoided by choice of design. However, a peel resistance of about 4 N/mm is sought for assurance.
Keeping in mind that today there are already around 250,000 adhesive formulas worldwide which are completely specialized in application, it becomes clear that there is hardly any other method of combining components as specialized as the adhesive industry. This is not only, but particularly, true in the aviation industry.
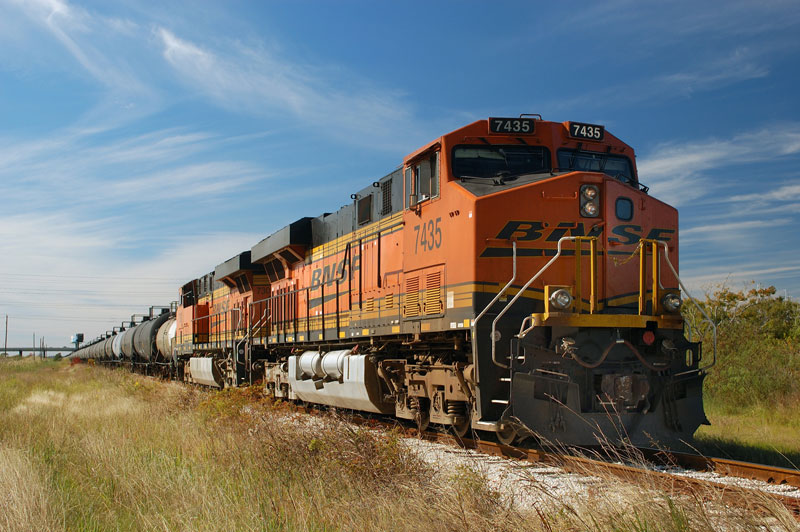
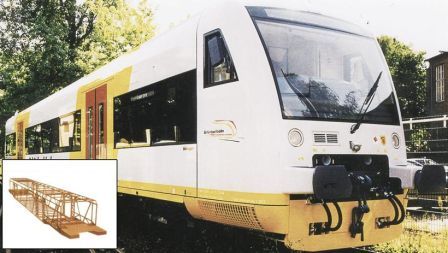
Rail Vehicle Maintenance
In rail vehicle manufacture, new components such as those made from glass-fiber reinforced plastic (GFRP) have resulted in enormous weight reduction and have transformed the production process. In Europe, ADtranz regional trains are manufactured using a frame structure consisting of tensile and compression struts in a triangular arrangement. This is the lightest design for bearing structures. Due to the frame structure, it is not necessary to weld on metal sheets to take up the shear stresses. There are only tensile and compressive forces in the struts. In order to enclose the frame, large outer skin elements are bonded to the supporting metal structure using moisture curing one-component (1-C) polyurethane adhesives. No complex straightening and filling work is required, as is the case when welding is used to attach the metallic outer skin elements. The GFRP elements that are used for the outer skin have a sandwich structure and hence provide good thermal insulation and have very good acoustic properties. As no heat distortion occurs, contrary to when welding, the outer skin gives the rail vehicle a ready painted/lacquered, level, smooth and flush outer surface with no additional work having to be undertaken.
Joining a metallic framework structure with components made of fibre reinforced composite plastic can only be economically and reliably achieved using bonding technology. In order to compensate the different linear deformations of the structure and outer skin when they are exposed to heat, a highly elastic, thick film of adhesive is used. The resulting bonds have high strengths, even when subjected to repeated temperature fluctuations in the range between -40°C and +80°C and under impact-like stress. They also have very good resistance to aging, even in moist environments. The thickness of the bonded joint varies between 4 and 18 mm. This depends on the size of the components, which can be up to 8.5 meters long and therefore subject the bonded joint to very high shearing deformation. Another advantage of this type of structure is the high damping and the positive effect this has on the dynamic operating characteristics and ride comfort.
All in all, these regional trains are about 25% lighter than comparable conventional trains, and they also have improved ride characteristics, lower production costs and reduced energy requirements for operation.
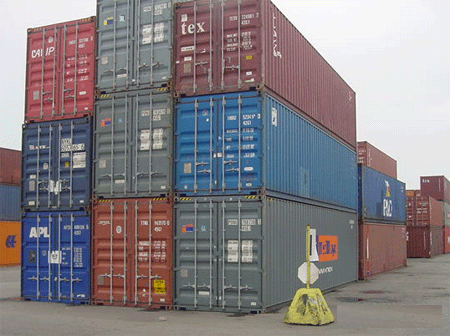
Container Construction
Sandwich panels are widely used for constructing containers and refrigerated containers. These panels are made by bonding core materials such as plastic foams, sheets made of mineral materials or honeycomb sheets to cover plates made of aluminium or glass-fiber reinforced plastic. Low and medium viscosity epoxy resin adhesives are used for this purpose and decorative panels also being bonded using such adhesives. Of late, MS polymers are also being increasingly used for this. They have good adhesion without prior application of a primer (even on lacquered/painted surfaces) and they have universal application because of their good elastic properties and high UV stability.
Looking to Source an Adhesive or Sealant for Your Application?
Try the Adhesive & Sealant Council's online Buyer's Marketplace.
This directory tool serves as a quick and efficient way for end users and industry manufacturers to find the right adhesive or sealant solution and the right partner for their application needs. Users can narrow their directory search by market segment, technology, raw materials, equipment or service needs. Try it now.
The Latest News & Innovations In The Transportation Market...
New Application Development Center in India
New Application Development Center in India Adhesive, sealant, and additives manufacturer, LANXESS, reports that it has opened a new 'India...
New Water-Based Pressure Sensitive Adhesive Uses Cylinder Application Method
New Water-Based Pressure Sensitive Adhesive Uses Cylinder Application Method A new fast-drying and water-based adhesive is available for lightweight...
New Adhesive Application Engineering Center & Manufacturing Site in India
New Adhesive Application Engineering Center & Manufacturing Site in India Henkel reports that it has launched a state-of-the-art Application...
New Waterproof, Bacteria-Resistant Bioadhesive Inspired by Mussel Mucas
New Waterproof, Bacteria-Resistant Bioadhesive Inspired by Mussel Mucas Marine molluscs cluster atop rocks and along the bottoms of ships, and hold...
Adhesive, Sealant & Coating Materials Company Named to America’s Greenest Companies List
Adhesive, Sealant & Coating Materials Company Named to America's Greenest Companies List A major materials supplier and manufacturing company in...
Major Manufacturer of Adhesives & Sealants Celebrates 90 Years
Major Manufacturer of Adhesives & Sealants Celebrates 90 Years Franklin International is celebrating 90 years of operation with their founding...