Assembly Operations Market
Explore the basics of this market plus articles, videos, webinars, selection guides, white papers, manufacturers and more…
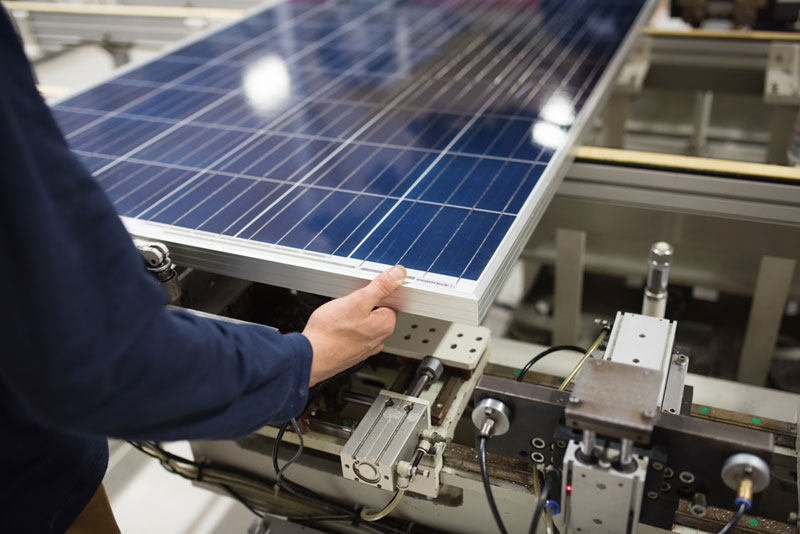
How adhesives are used in the assembly market...
The assembly market counts on adhesives and sealants to address many of their application needs. From appliances and electronics to textiles and sports equipment, the assembly of materials involves precision and numerous complexities, especially as it relates to the bonding of dissimalar materials. Adhesive solutions help keep production output and quality high while addressing evolving trends.
Assembly adhesives are designed to meet the most stringent requirements in today’s fast-moving world, enabling improved operational efficiencies, increased sustainability levels, enhanced design options, and increased product performance and durability.
The Assembly Operations market includes applications such as:
- Sandwich Panel Manufacturing
- Appliances and Electrical/Electronic Products
- Mechanical Equipment
- Flexible Materials
- Medical Applications
- Solar Applications
- Heating, Ventilation, Cooling (HVAC)
- Sports Equipment and Toys
- Abrasives & Filters
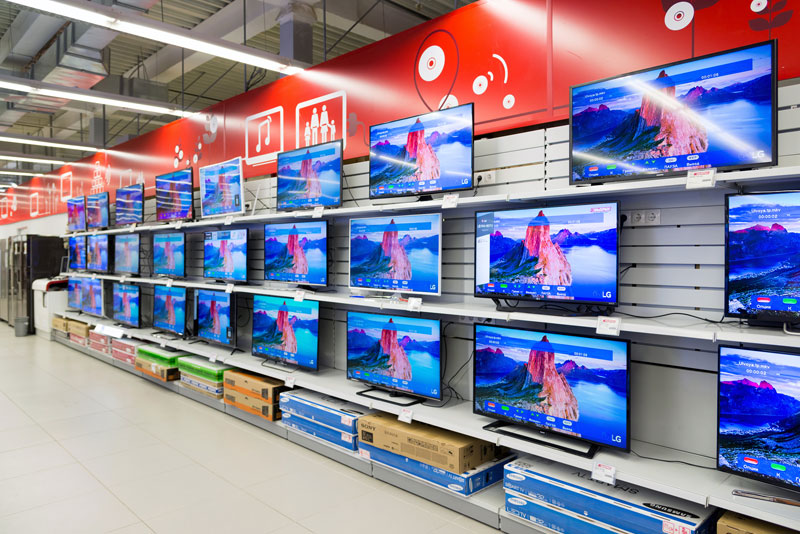
Electronics
The Electronics Market is generally defined as anything containing a microprocessor chip, including but not limited to:
- Cell Phones and Personal Devices
- Computer Hardware
- Cameras & Video Device
- Televisions & Monitors
- Radio Device
- Anything containing a Printed Circuit Board
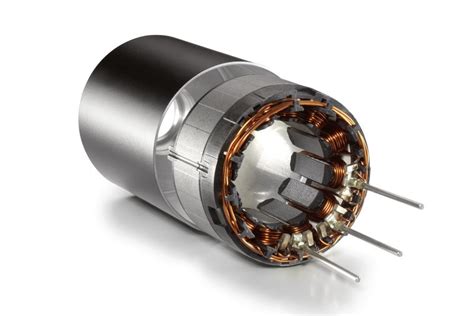
Electric Motors
A whole host of electrical devices, from kitchen appliances to CD-players and video cameras, contain electric motors. These mass-produced motors are expected to have precise synchronization and a long lifetime.
Adhesives are indispensable in motor assembly, for example for connecting the armature and shaft, for connecting the commutator and shaft, for attaching ball-bearings and for securing screws in position. The preferred type of adhesive for this is an anaerobically curing acrylate adhesive, namely an acrylate adhesive that cures when oxygen is excluded
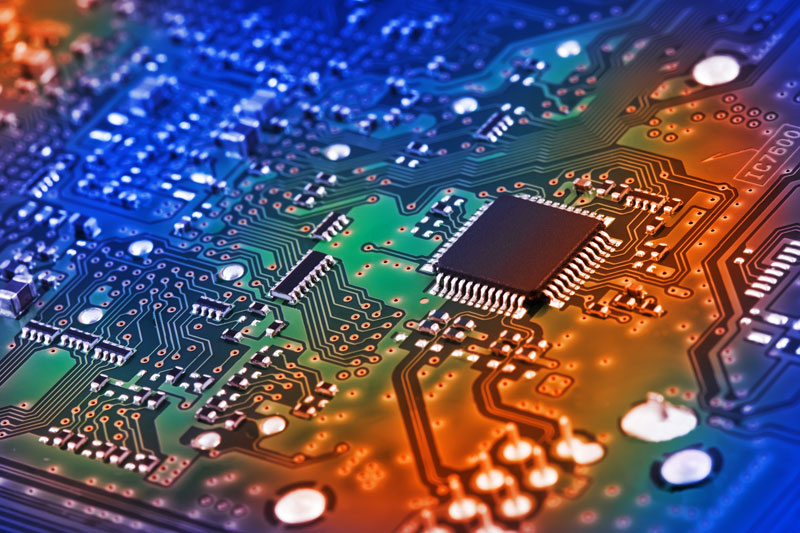
Electronic Circuits
From the very outset, the rapid developments in the area of electronics have involved ever smaller components and ever greater circuit complexity. The continuing miniaturization has not only resulted in smaller components but also components that are more sensitive to heat. For cost reasons, it was also necessary to reconsider the methods used to assemble printed circuit boards (PCBs). The solution to these problems was advanced bonding technology. Adhesives have hence taken over many tasks in the assembly of electronic circuits. Besides being used for mechanical attachment, they also function as for example electrical conductors and insulators. Today, many electronic components are fixed in their intended positions with adhesives, prior to soldering.
Single-component paste-like epoxy resin adhesives are used. These adhesives bond in 3 minutes at 120°C. Acrylate adhesives are used to a lesser extent. The latter are pre-cured by UV light to allow rapid fixing. Their final strength is then developed by applying heat.
Electrically conducting adhesives are normally epoxy resin adhesives containing a very small amount of ionic contaminants. To a lesser extent special polyimide adhesives are also used. In both cases these adhesives contain 70 to 80 weight percent of very fine silver powder. They are used when components cannot be soldered due to their sensitivity to heat, especially when repairs are being carried out. In addition, adhesives with heat conducting properties (e.g. adhesives containing high amounts of aluminium oxide) are growing in importance due to the increasing requirements on the heat management of circuits.
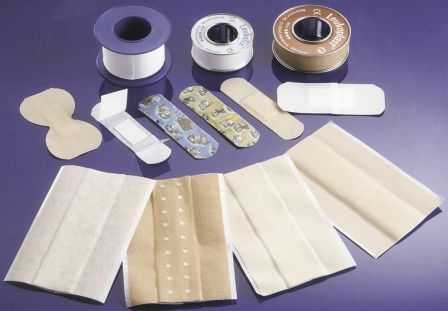
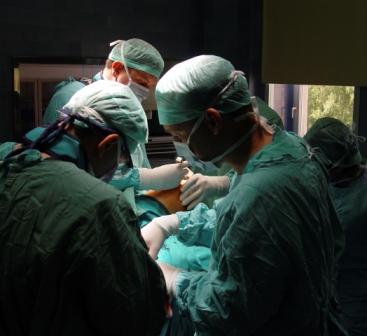
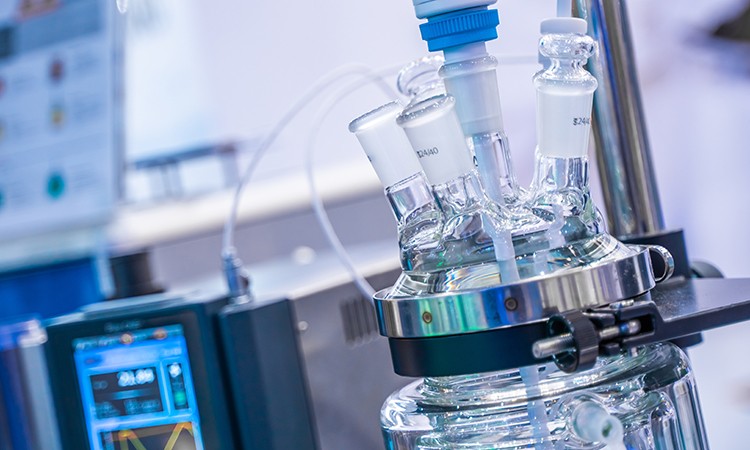
Medical Devices
The use of adhesives in medical applications was for a long time restricted to the manufacture of self-adhesive bandages (plasters, self-adhesive strips of fabric, etc.). The first pressure sensitive adhesives used for this were based on natural rubber. This was in part later superseded by synthetic rubbers (e.g. polyisoprene, polyisobutylene). In the middle of the 20th century, pressure sensitive adhesives based on polyacrylic acid esters became increasingly important, both for general use and for bandage materials.
Adhesives are today employed in diverse areas of medicine, replacing traditional methods with “friendlier” processes. In many cases, for example, stitches can be avoided by applying special cyanoacrylate adhesives to quickly close skin wounds. An advantage here is that the whole wound can be covered, so largely suppressing secondary bleeding and the risk of infection. Cyanoacrylic acid butyl ester is normally preferred over the methyl and ethyl esters because it cures more slowly and the polymerisation produces less heat; it also causes less tissue irritation. By and large, this adhesive is only used for relatively small wounds and occasionally in vascular surgery.
Consider the transdermal patch…where the drug delivery mechanism to the blood stream is through the skin. Adhesives enable a more efficient method of drug delivery rather than prescribing a high-ingestion dosage (which is subsequently flushed out of the body by the liver). Transdermal patch technology is highly effective because the adhesive that sticks the patch to your skin – made of products of chemistry like acrylic, acrylic-rubber hybrid, polyisobutylene and styrenic rubber solution – actually controls the rate at which the drug enters the body. This ensures that the drug dosage is continuously and evenly administered throughout the day, without the spikes and falls associated with medicines taken orally.
The applications are many…smoke cessation, hormone replacement, and cardiovascular aid (I.e. nitroglycerin delivery) are commonplace. New transdermal patches hit the market every day with more items like pain cessation becoming a reality. Other innovative products such as foot care and cosmetic patches, and nasal dilator strips have hit the market in recent years all possible because of the unique functional properties of the pressure sensitive adhesives integral to the product.
One of the newest bioadhesives on the market enables drugs to be delivered through the inside of the mouth, nasal passages and other mucus membranes instead of just through skin. It adheres extremely well to the soft, wet mucus membranes of the body because of adhesives made from starch-polyacrylic acid blends, which then completely erode and disappear. Drug makers are able to put their medicine into tablet, film or powder form, and the patient is able to attach the product directly to a mucus membrane, providing a means for controlled delivery of drugs to specific areas of the body or systemically (throughout the body).
In heart surgery, fibrin (made from fibrinogen), a soluble protein recovered from blood, is a key sealing agent having a haemostatic effect. Compared to cyanoacrylates, fibrin is gentler to body tissue but before use it must undergo a special treatment to prevent germs being spread. The use of methacrylate based adhesives has been a great success in orthopaedics for anchoring hip socket implants to the bone (see figure below). There are currently no other types of adhesive used for this application. The adhesive products comprise a.) a powder component (a mixture of polymethyl methacrylate and a polymerisation initiator) and b.) a liquid component (whose main components are methyl methacrylate and a polymerisation accelerator). Although this type of adhesive puts a not inconsiderable stress on bone and tissue due to the strong heat development, hip and knee implants anchored using this adhesive are in 90 percent of cases functional for about 15 years.
In dentistry, fillings based on UV curing acrylates have largely replaced traditional filling materials such as amalgam. The products have a long open time (the period during which they can be used after mixing) and bond in just a minute or so when exposed to UV light.
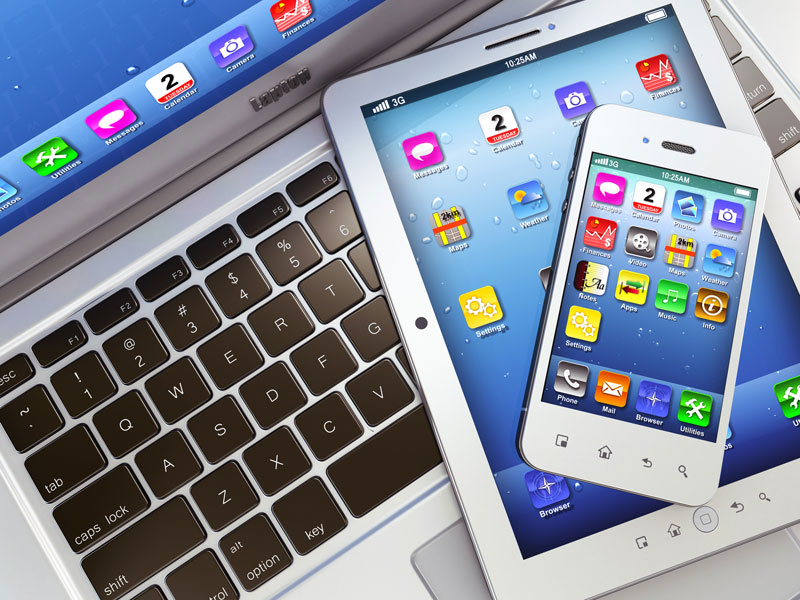
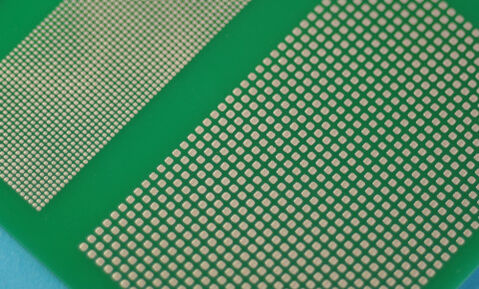
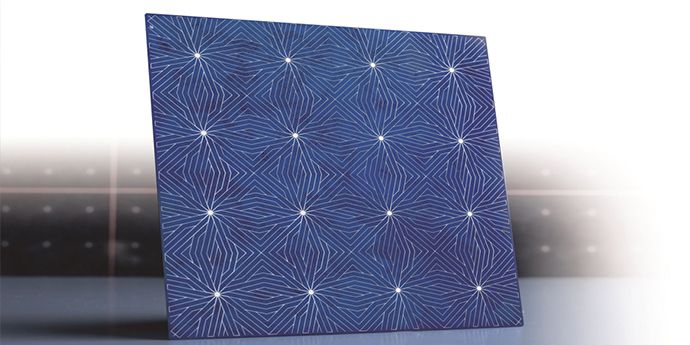
Cell Phones & Devices
Some inventions become indispensable within a very short time. And the cell phone is one of them. How did we ever get along without them? Hardly anyone had one in the 1980s, but by the end of the 1990s they were everywhere. Now, one is always within easy reach. But nobody realizes that up to 21 different types of adhesive foil are used in cell phone production today.
The cell phone has been an indispensable tool of daily life since the late ’90s. Business people on the go are reachable thanks to cell phones; if an accident happens, help is just a phone call away; if you are running late, a quick text message keeps your friends and family informed.
But why are cell phones getting cheaper, better and smaller?
The answer is simple: Adhesives
What modern adhesive films, composed of epoxy resin, silicone or polyurethane, can accomplish is amazing. You can produce electrical connections between two or more contact points or replace small screws and solder joints. The bond is flatter, less complex and cost-intensive. In comparison to solder joints, adhesive film is lead free and less vulnerable to heat, thereby reducing the risk of thermal damage.
There are two types of electrically conductive adhesive film:
Isotropic conductive adhesive: In this type of adhesive film, the current can flow in all directions. This is how it works: Electrically conductive adhesive particles are pressed into the contacts during the drying process,allowing an electrical connection. The minimum distance between two contacts is only 0.035 mm. Incidentally, isotropic conductive adhesive film is used in EMI shielding (electromagnetic interference).
Anisotropic conducting adhesive: This type of adhesive film allows power to flow in only certain directions. Micro-particles are embedded in the adhesive, which are compressed between two contact points, simultaneously generating insulation between the individual points.
Further adhesive film in cell phones protects against shock and prevents the permeation of moisture. And adhesive film protects the screen from unpleasant scratches, ensuring untarnished communication.
Looking to Source an Adhesive or Sealant for Your Application?
Try the Adhesive & Sealant Council's online Buyer's Marketplace.
This directory tool serves as a quick and efficient way for end users and industry manufacturers to find the right adhesive or sealant solution and the right partner for their application needs. Users can narrow their directory search by market segment, technology, raw materials, equipment or service needs. Try it now.
The Latest News & Innovations In The Assembly Market...
European Tape Conference – An In-depth Learning & Networking Opportunity
European Tape Conference - An In-depth Learning & Networking Opportunity In September of 2024 the European Adhesive Tape Association (Afera), is...
Adhesives Manufacturer Recognizes Customers’ Innovations in Solar, Roofing, Sanitary Products
Adhesives Manufacturer Recognizes Customers' Innovations in Solar, Roofing, Sanitary Products H.B. Fuller, a large adhesives and sealants...
Adhesive & Sealant Manufacturer Wins Electric Sustainability Impact Award
Adhesive & Sealant Manufacturer Wins Electric Sustainability Impact Award Schneider Electric, a provider of process and energy technologies,...
New Alignment Adhesive for Automotive Camera-Module Bonding Applications
New Alignment Adhesive for Automotive Camera-Module Bonding Applications Henkel has launched a 1-step UV-cure epoxy adheisve for high resolution...
New Two-Component CO2-reducing Packaging Solution for Adhesives & Sealants
New Two-Component CO2-reducing Packaging Solution for Adhesives & Sealants A new adhesive and sealant filling, labeling and transportation...
Adhesive Tape College Successful in Munich, Bringing Together European Industry
Adhesive Tape College Successful in Munich, Bringing Together European Industry Adhesive tape technology is one of the key technologies of the...