Surface Treatment
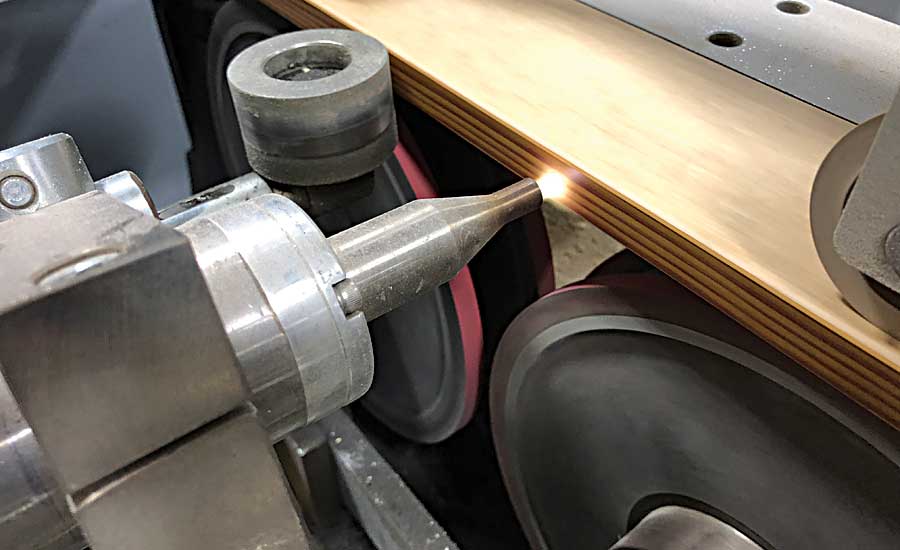
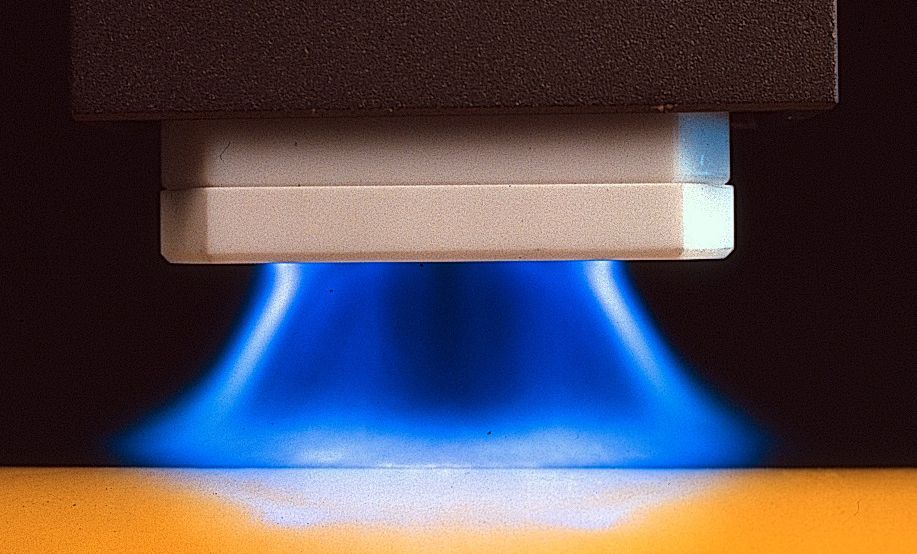
Types of Surface Treatment
There are three broad types of “surface treatment”…
Surface preparation – covers cleaning (degreasing) and preparation (e.g. deburring) of the substrate surface.
Surface treatment – encompasses all mechanical processes (e.g. grinding, jet-cleaning), chemical processes (Metals: e.g. etching; Plastics: e.g. gas-phase fluorination) and physical processes (Plastics: low pressure plasma) that alter the structure and/or chemical composition of the surface, relative to the starting base material. As an example, the surface pretreatment of polyethylene is mentioned here. Without such pretreatment polyethylene is difficult to bond.
The technique used for this pretreatment is the so-called corona method. In order for example to improve the adhesion properties for the manufacture of laminated films, electrical discharges in the presence of atmospheric oxygen at voltages of up to 60,000 volts are allowed to act on the materials.
Surface post-treatment covers all techniques that serve to preserve the treated surface, e.g. application of a primer.
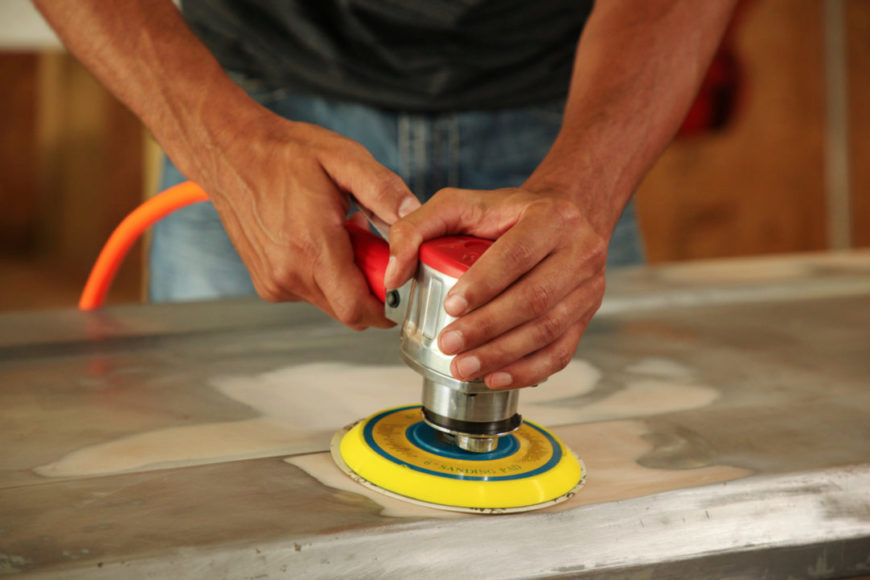
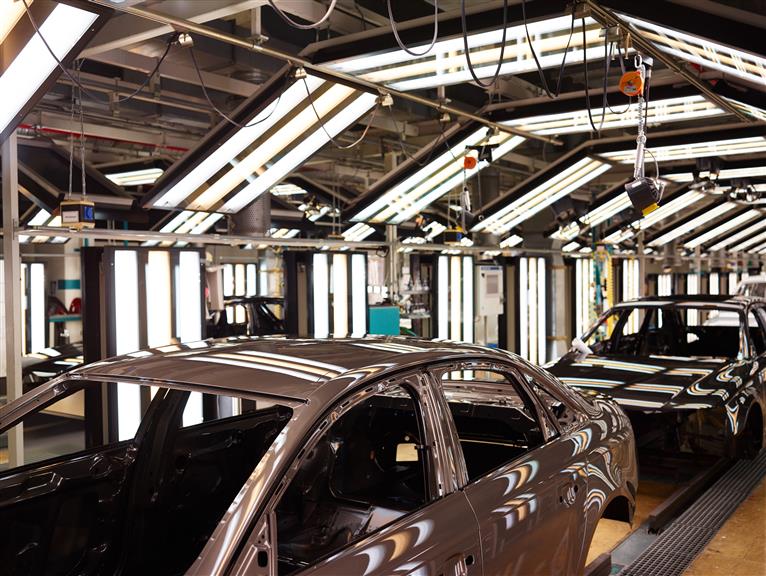
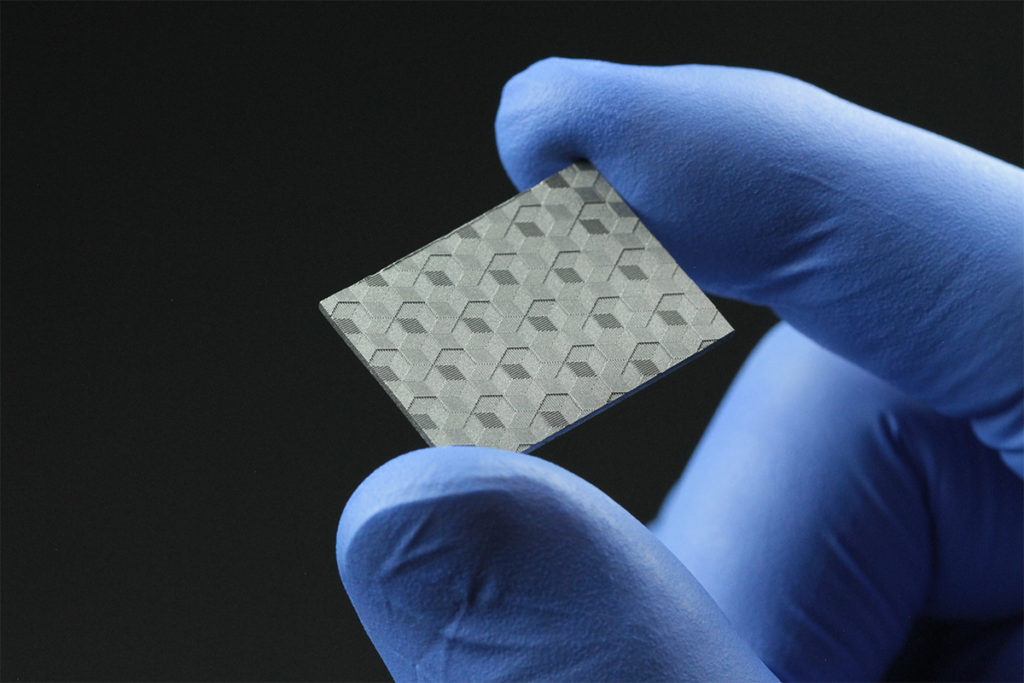
Substrate Surface Critical to Bonding
Certain requirements have to be met by the structure of the substrate if a high-quality, strong bond is to be achieved:
1. The substrate surface must have good wetting properties, namely the chosen adhesive should not form beads on the substrate surface but must rather distribute itself (spread) across the surface.
2. The substrate surface must have good bonding properties, namely there must be intermolecular and chemical interactions with the adhesive molecules.
3. The surface layer of the substrate must be securely attached to the substrate. Imagine for example highly rusted steel supports that have to be bonded together. If the surface rust layer is not removed, then rust is merely bonded to rust. On subjecting the substrates to loads, the rust breaks away together with the adhesive. In contrast to rust, the oxide layer on aluminium is very strongly attached to the base material and is a good base surface for adhesion.
4. After the bonding process, the surface must not change in an uncontrolled way. Ground steel, for example, rusts – even under the adhesive film – if the bond is in a moist environment. In order to create a bond having good long-term stability, solely grinding the steel surface is inadequate – and in addition suitable measures must be taken to prevent rusting under the adhesive film when using this steel component in a moist environment.
These facts emphasize the need for subjecting the substrate to a surface treatment, to create a surface that meets the criteria. In general this means treating the materials such that:
– In a production environment, conditions for bonding are created that guarantee reproducible bond quality;
– Wetting and adhesion are improved;
– The long-term stability of the bonded joints is improved.