Thermal Joining
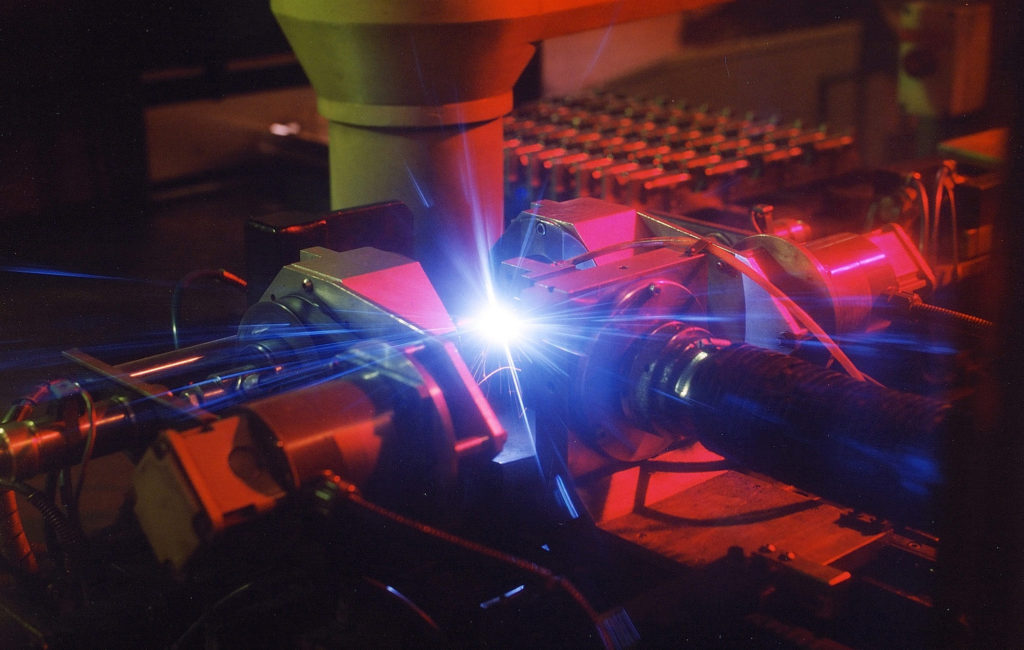
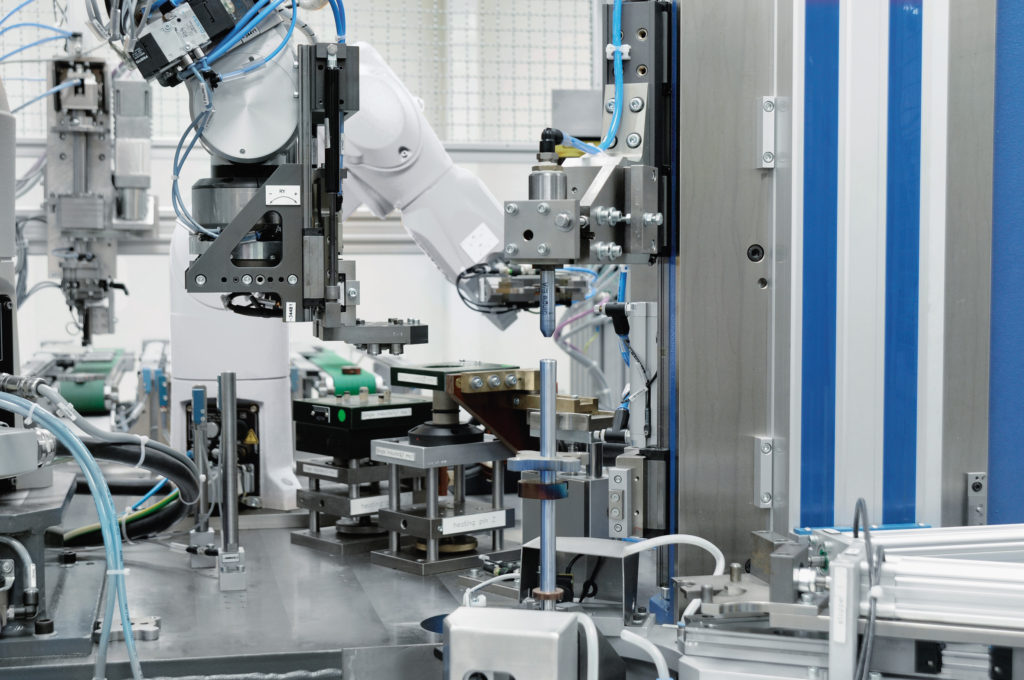
Thermal Joining Methods vs. Adhesive Joining…
Thermal joining primarily includes welding, soldering, and brazing. This method of joining is only effective on homogeneous metal substrates with similar melting points. Thermal methods of assembly are very difficult to disassemble and can result in aesthetic concerns such as distortion and discoloration. By grinding or sanding down the substrate to minimize the metal bump or discoloration, and painting over the problem area, if necessary, manufacturers can often solve these aesthetic concerns. Distortion, which is caused by uneven heating and cooling of the part, is more difficult to repair.
Welding, while typically less visible than fastening, can distort or heat warp the metal and weaken the alloys. It can burn off galvanized metal’s corrosion protection. It often requires finishing once joined.
There are many advantages in using adhesives compared to thermal bonding methods like welding, brazing and soldering, as listed below.
- Surface Area—For a lap joint the stress is distributed over a relatively large area. This provides a strong joint with lower specific stresses.
- Provide ability to join dissimilar substrates.
- Allow for thinner and lighter materials of construction.
- Allow for high-speed assembly and for a high production process, an adhesive joint can be extremely economical.
- Afford ability to precisely realign parts after initial connection.
- Allow for thermal expansion of component parts and compared to welding there are no high temperatures required.
- Eliminate read-through, burn marks, and discoloration.
- Eradicate part distortion caused by thermal joining methods.
- Eliminate need for secondary operations (e.g., grinding).
- Avoid unwanted visible joint lines.
- Improve appearance by color matching bond lines or using paintable adhesives.
- Possibility of joining objects after they have been painted.
- Reduce need for clamps, fixtures, and jigs.
- Decrease the need for surface preparation.
- Many adhesives are electrically insulating and this prevents galvanic corrosion. It also enables the isolation of an electric circuit from the rest of the assembly.
- Adhesives simplify assembly by replacing several fasteners with a single bond or by allowing several components to be joined in one operation and eliminating fasteners, thus lowering product weight.
- Adhesives are also good for joining sensitive materials. Adhesive bonding does not require high temperatures and many adhesives cure at room temperature. If the materials are heat-sensitive, prone to distortion, or have different coefficients of thermal expansion, they can be joined by adhesives rather than by welding.
- Possible to improve product design with new materials.
- Join dissimilar substrates with ease including non-metallic substrates to metal.
- Enable use of thinner, lower gauge metals.
- Reduce Noise, vibration and harshness.
- Retain thermal and electrical conductivity.
- Limit risk of corrosion.
- Produce environmentally friendly products.
- Facilitate easier recycling.
- Achieve cleaner, more convenient disposal.
- Enable reduced waste via custom formulations.
Explore the different types of fastening: